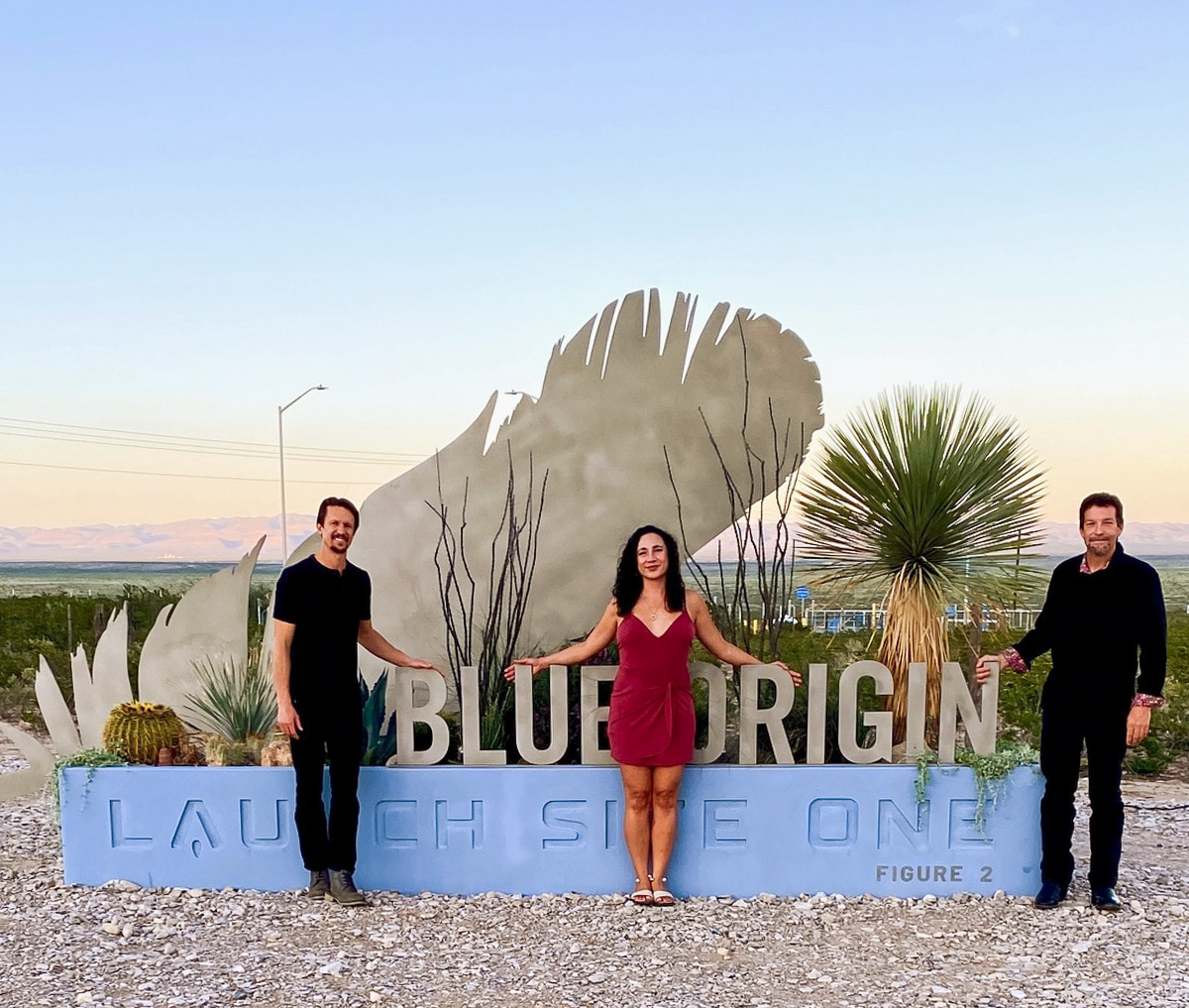
Marfa Cement Works creates stunning welcome to Launch Site One
By Shanna Cummings
The entrance to Blue Origin Launch Site One wasn’t hard to miss.
In fact, until a couple of weeks before the space tourism company’s first manned flight this summer, an unsuspecting driver on Hwy 54 could have zoomed past the lonely road and single gatehouse without a second thought, entranced by the mountains and rugged desert landscape.
But with the final countdown to owner Jeff Bezos’s liftoff came the need for a visual statement to welcome visitors and launch spectators. The commission was awarded to husband and wife team Thomas Lancaster and Bella Pena of Marfa Cement Works.
The pair usually specialize in art pieces cast in glass fiber reinforced concrete, or GFRC, created in their shop. The Launch Site One project would provide a challenge in size, material, time, and location. The original rendering provided by Blue Origin specified both the planter and the signature feather cast in GFRC, which wasn’t possible in the short turnaround time. While brainstorming ways to make their firm stand out from their competition, Lancaster and Pena decided to offer Blue Origin blue concrete for the planter, and Pena had another idea for the feather.
“I’m a welder, a metal fabricator,” she said. “So I thought, let’s do the feather in stainless, and do a matte finish.”
“We didn’t have enough time to build a feather out of concrete,” Lancaster said. “But we also felt stainless was a better material for that part of the project.”
The clock was ticking. Once the project was approved and the legal requirements met, the team had 25 days until the early July deadline. Finding a sheet of stainless steel large enough took a week, designing and cutting the feather took another week before Pena and Bubba could begin welding.
The substitution may not mean much to a layman, but using stainless steel required special welding materials and conditions to ensure the 2,000-pound feather – cut from a single sheet of half-inch stainless steel – didn’t bow during the welding process.
“Stainless warps really easy when you add heat to it, and we were welding everything to one side,” Pena’s welding mentor Bubba Bergeaux said. “It’s just a different kind of metal to use.”
A special table was built at Bergeaux’s shop to hold the feather while Pena and Bergeaux worked, and the shop was cleaned and retrofitted specifically for working on stainless steel, to prevent contamination from regular steel, which would rust when exposed to the elements.
“It’s a big deal because it’s a really hard metal to work with,” Bergeaux said. “You can mess stuff up fast. You can warp that whole thing and make it just look like junk.”
“We couldn’t screw up,” Pena said.
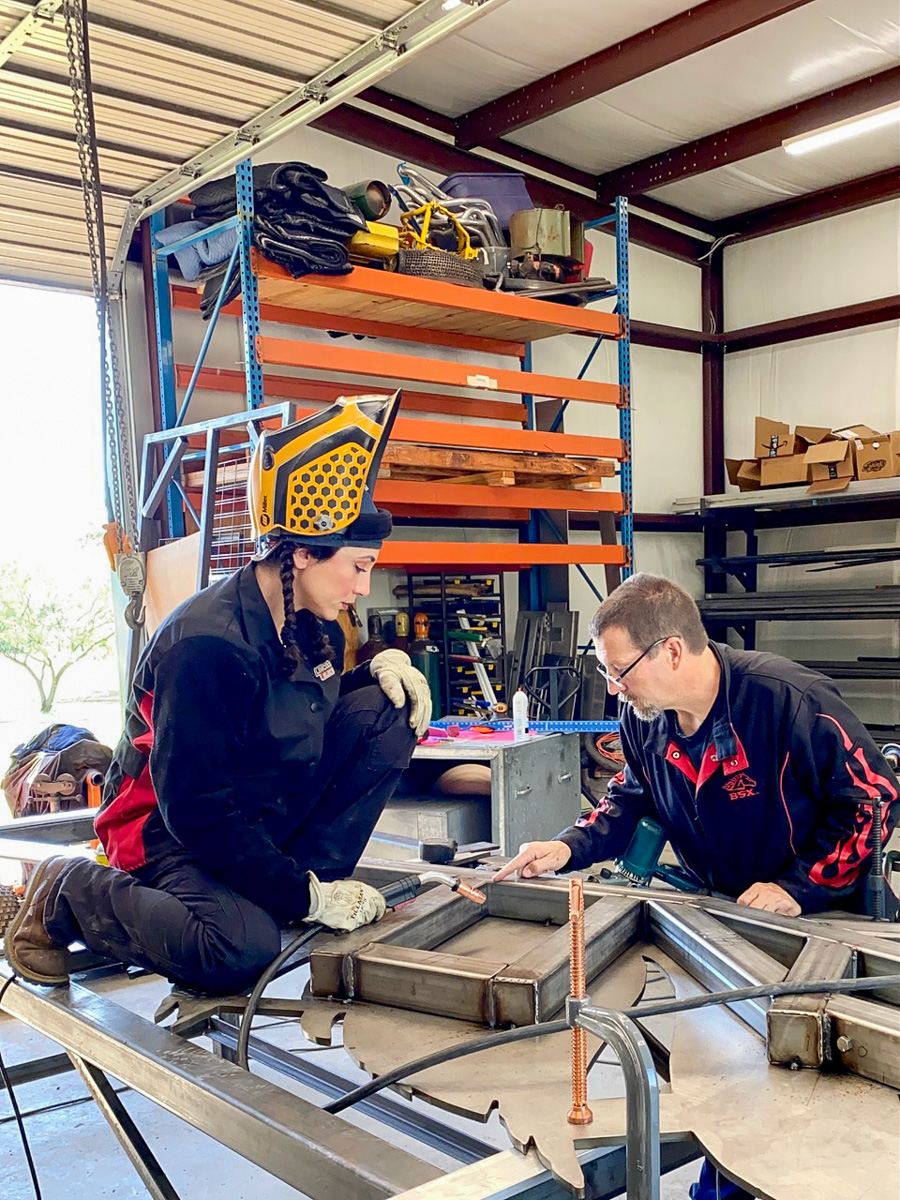
Working with stainless steel could be tricky for a seasoned welder. When Pena suggested it, she not only hadn’t worked with stainless steel before, she also had been welding for only eight months. She began initially as a way to keep welding work within the business, but quickly discovered she not only had a talent for it, but wanted to pursue it full time. She learned first from retired Border Patrol Agent Frank Lopez in Alpine before meeting Bergeaux. She said she wanted to learn from someone experienced with stainless rather than subcontracting that part of the project. She personally performed half of the welding work on the feather.
While working on the feather, Pena and Bergeaux often worked 12 hour days in sweltering Dallas summer humidity.
“You can’t have a fan or anything when you’re welding, and you have all this gear,” she said. “We’d lift up our hoods and would just be dripping sweat and I loved every minute of it.”
If done incorrectly, the heat of welding can make stainless steel blister, ruining the appearance. Because of the size and weight, Pena and Bubba couldn’t lift the feather to look at the front face until after they had finished welding. To their relief, it was fine.
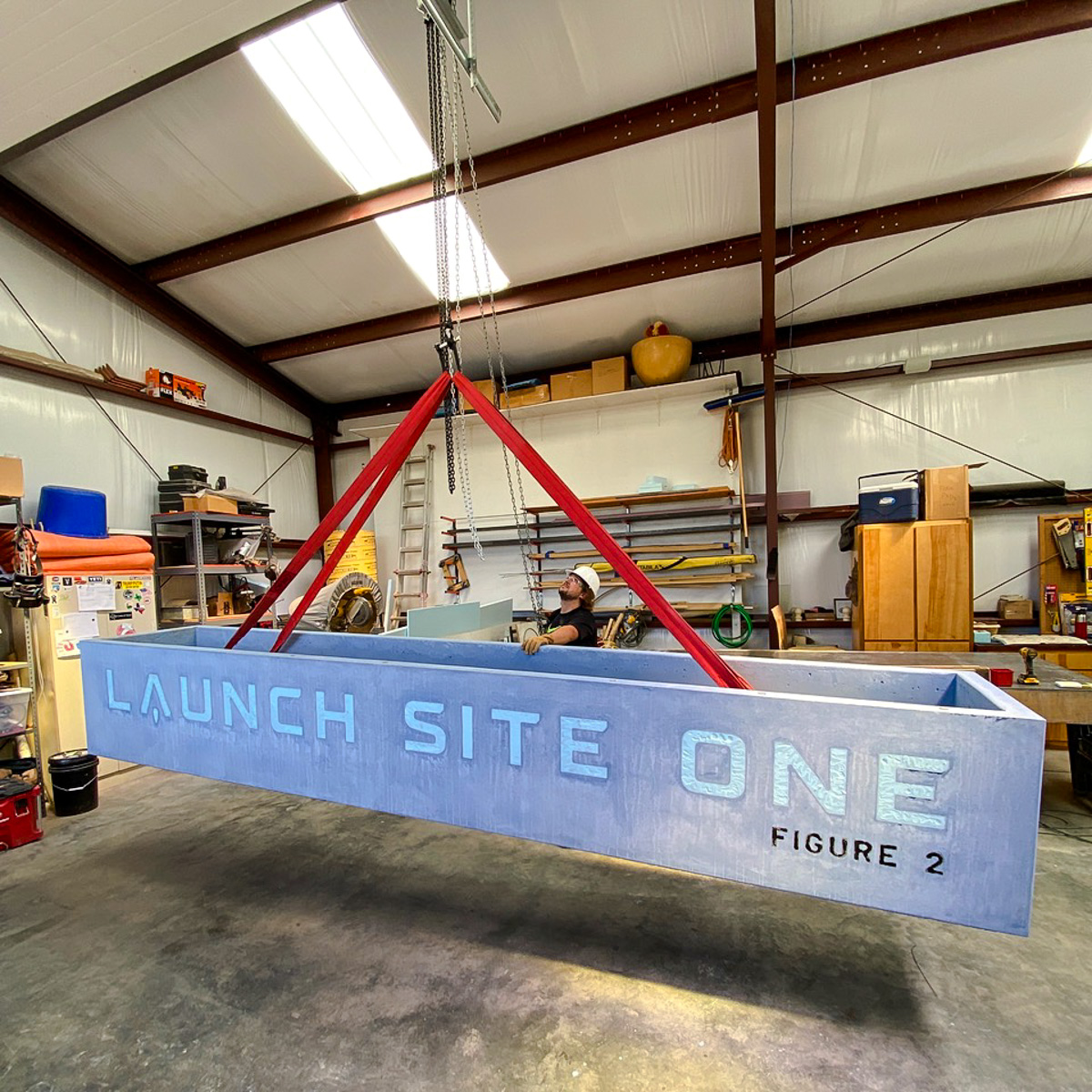
Once welding was completed and the feather transported to West Texas, preparing the site at Launch Site One entrance and setting up the planter and feather were the last steps, completed in six days of 100-degree summer heat. In order for the feather to withstand the high winds common to the desert, the team mounted it to three eight-foot piers set into the ground. Pena and Bergeaux had affixed flanges to the feather, and the piers needed to be set exactly for the pieces to fit together as designed. Neither the piers nor the feather could be altered in time if either had been incorrect.
“Everything came out really perfect with this project,” Pena said.
The planter was then filled with native desert flora selected by Pena for the landscaping. Blue Origin employees leaving at the end of their shift admired the finished product, taking pictures like tourists, Pena said.
“They were really happy and said, ‘You don’t know how nice it is to have something beautiful,’” she added.
Despite the short timeline, the project was completed two days ahead of schedule.
Throughout the process, Pena and Lancaster were prohibited from advertising their involvement in the project due to the Non-Disclosure Agreement they signed at the beginning. They were only recently granted permission to claim it publicly.
“And that meant a lot to me as a new welder and metal fabricator,” Pena said. “Because I was the one that did every part of this project. And it meant a lot to me,” she continued. “And I really wanted to use something like this to go into the public art scene and to create pieces more for commercial, you know, public art settings.”
Pena said she plans to keep working on her welding and metal fabrication skills under her business, Unity Fabrication, perhaps next working with Corten steel.